Blog
Unlock the potential of digital transformation for your supermarket with our groundbreaking trade solutions designed for retailers. Streamline operations, optimize supplier relationships, enhance customer experiences, and boost profitability in a single platform.
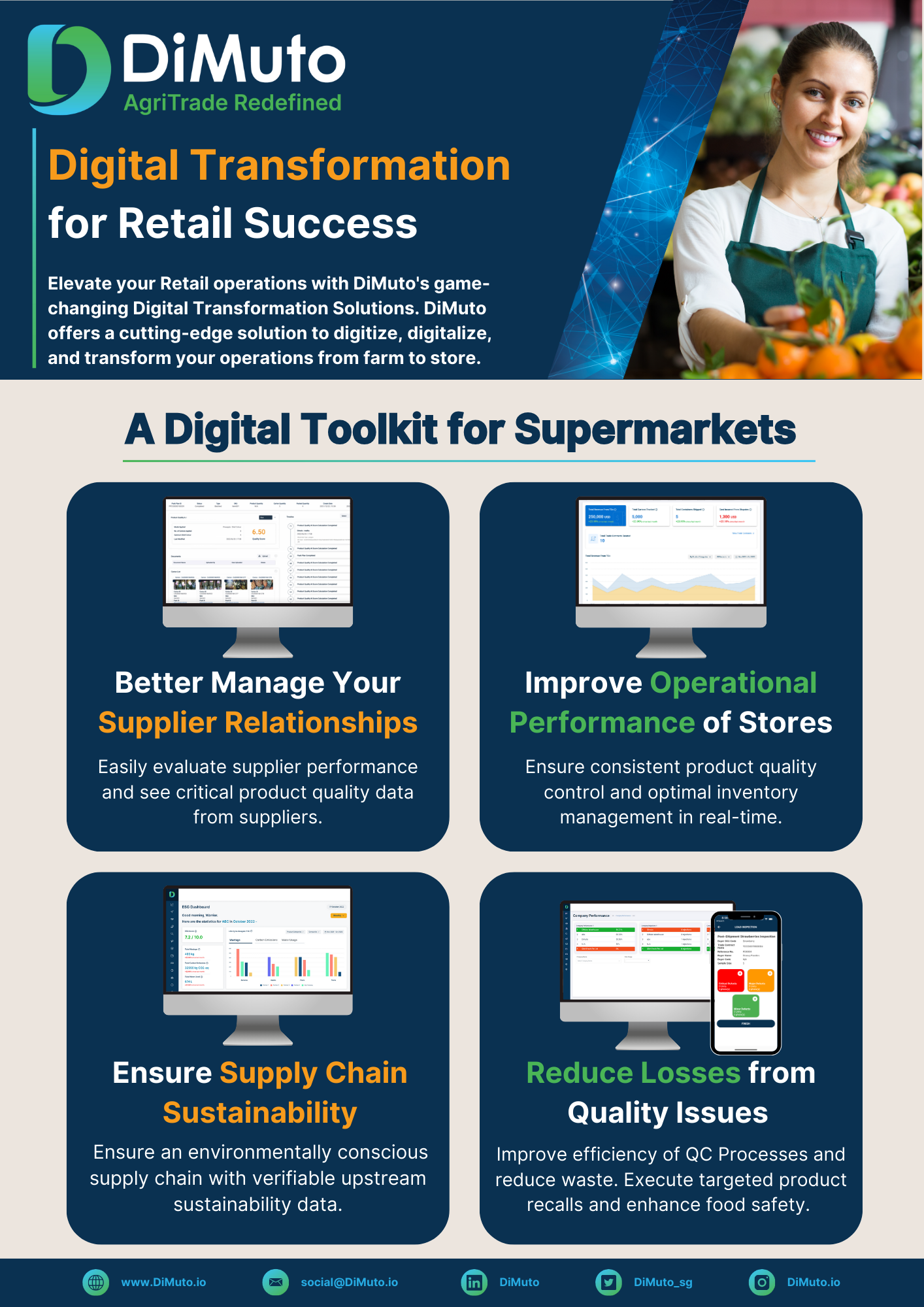
Download the DiMuto For Retailers One Pager here.
Welcome to a new era of trade efficiency and transparency. DiMuto offers a suite of comprehensive trade solutions designed specifically for importer-wholesalers like you, streamlining your operations and enhancing your competitive edge:
- End-to-End Visibility: Gain unprecedented insight into your supply chain from source to shelf. Track, trace, and verify the authenticity of your products with ease.
- Automated Compliance: Seamlessly navigate the complex landscape of regulatory compliance. Dimuto’s solutions ensure that your imports meet all necessary standards and certifications.
- Efficient Documentation Management: Say goodbye to cumbersome paperwork. DiMuto’s platform simplifies and digitizes documentation processes, reducing administrative burden.
- Smart Inventory Management: Optimize your inventory with real-time data and predictive analytics. Make informed decisions that drive profitability and reduce waste.
- Market Access Expansion: Explore new markets and partnerships with confidence. DiMuto connects you with a global network of trusted partners, opening doors to new opportunities.
Elevate your trade operations and join us in revolutionizing the way you do business today.
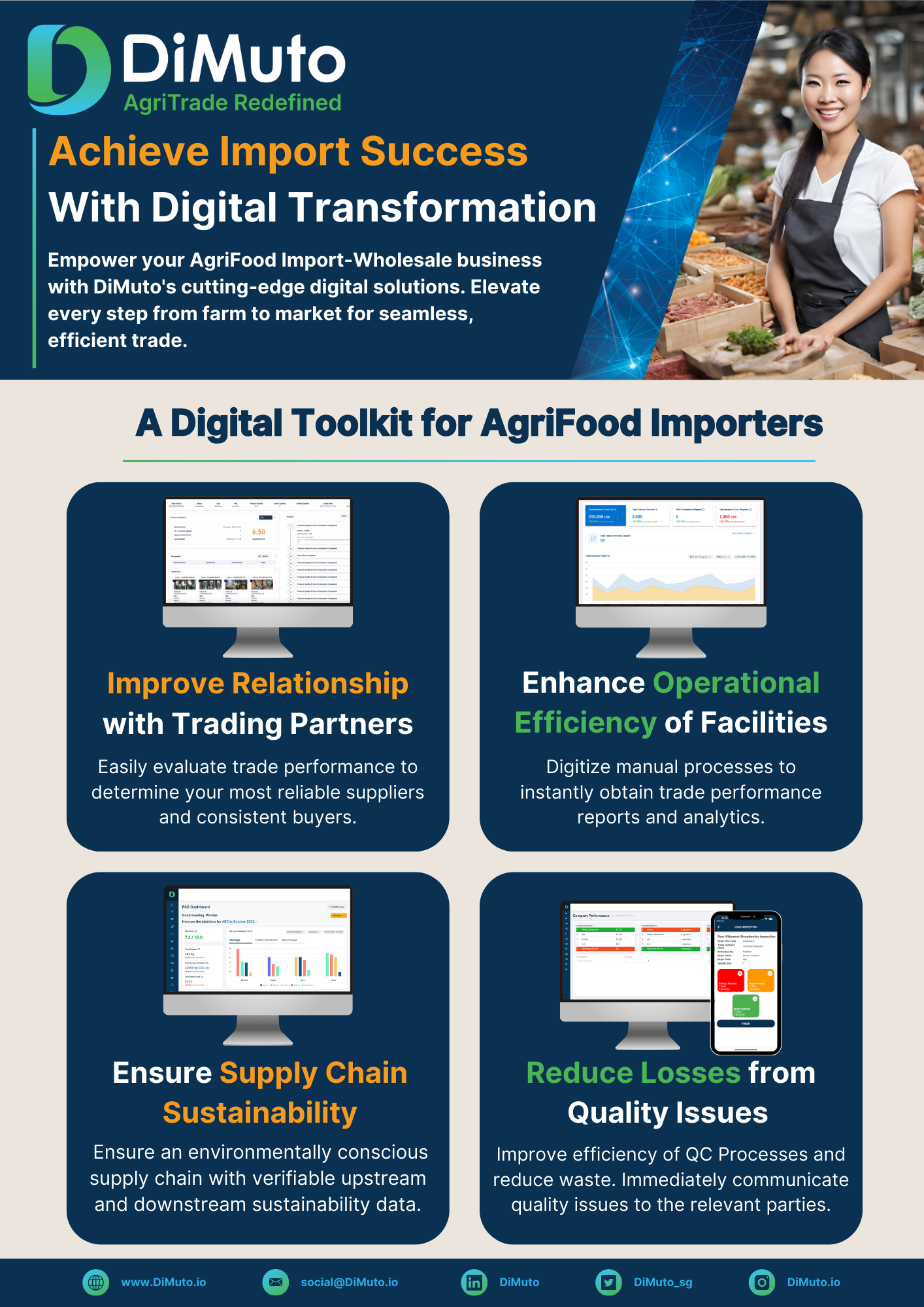
Download the DiMuto For Importers-Wholesalers One Pager here.
Welcome to a transformative approach to AgriFood trade. DiMuto offers a suite of powerful trade solutions curated for agrifood traders, designed to amplify efficiency, transparency, and profitability.
- End-to-End Visibility: Gain unprecedented insight into your supply chain from source to shelf. Track, trace, and verify the authenticity of your products with ease.
- Automated Compliance: Seamlessly navigate the complex landscape of regulatory compliance. Dimuto’s solutions ensure that your imports meet all necessary standards and certifications.
- Efficient Documentation Management: Say goodbye to cumbersome paperwork. DiMuto’s platform simplifies and digitizes documentation processes, reducing administrative burden.
- Smart Inventory Management: Optimize your inventory with real-time data and predictive analytics. Make informed decisions that drive profitability and reduce waste.
- Market Access Expansion: Explore new markets and partnerships with confidence. DiMuto connects you with a global network of trusted partners, opening doors to new opportunities.
Elevate your trade operations and join us in revolutionizing the way you do business today.
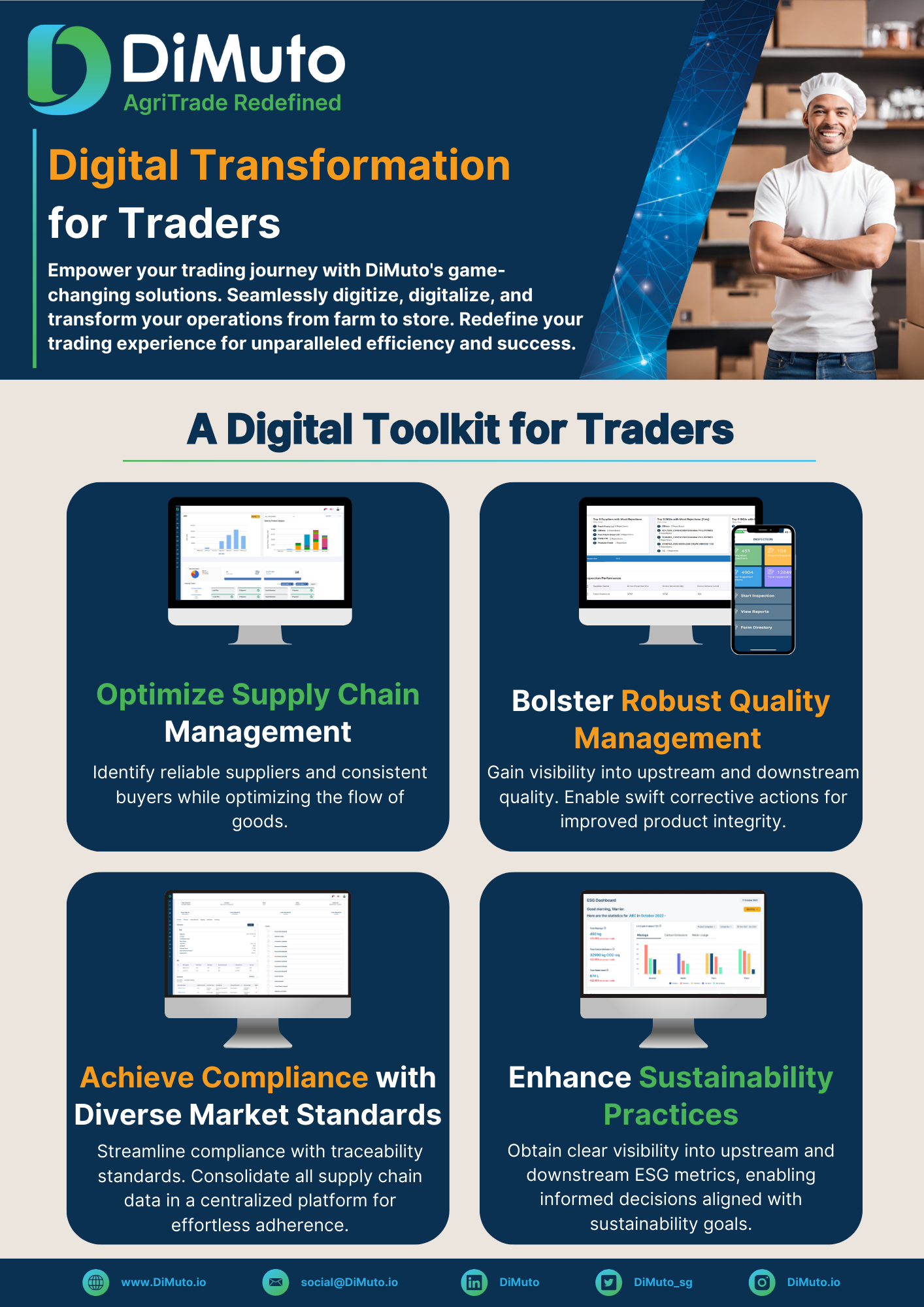
Download the DiMuto For Traders One Pager here.
Welcome to a revolutionary approach to AgriFood trade. Dimuto offers a suite of powerful trade solutions curated for grower-exporters, designed to enhance efficiency, transparency, and profitability.
- End-to-End Transparency: Gain unprecedented visibility into your supply chain, from cultivation to export. Trace, verify, and ensure the integrity of your products at every step.
- Seamless Regulatory Compliance: Navigate regulatory complexities with ease. Dimuto’s solutions ensure that your products meet all required standards and certifications, ensuring smooth export processes.
- Simplified Documentation Management: Bid farewell to paperwork hassles. DiMuto’s platform digitizes and streamlines documentation, saving you time and resources.
- Intelligent Crop Management: Optimize your crop yield with real-time insights and predictive analytics. Make informed decisions that enhance profitability and reduce waste.
- Global Market Expansion: Explore new markets and establish strategic partnerships with confidence. Dimuto connects you with a global network of trusted partners, opening doors to new opportunities.
Elevate your grower-exporter operations and partner with us in shaping the future of the industry. Download now to unlock the full potential of your agrifood trade with Dimuto’s innovative solutions.
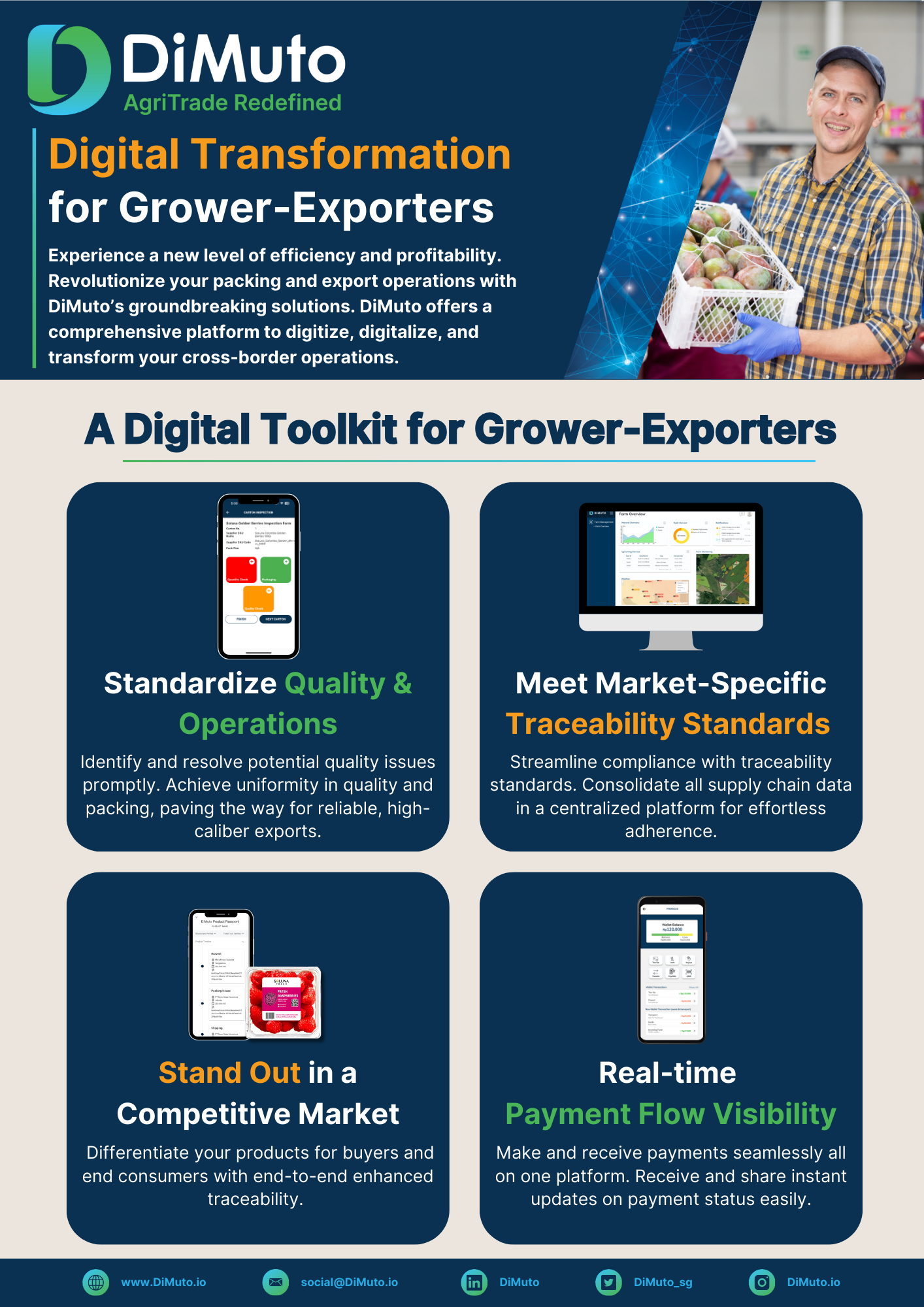
Download the DiMuto For Grower-Exporters One Pager here.
Welcome to a new era of Agribusiness financing. DiMuto Financial Services revolutionizes how financiers engage with the agricultural supply chain, offering a suite of tools designed to optimize sustainable investments and ensure growth. Find out how you can leverage primary data and AI for ESG investing today.
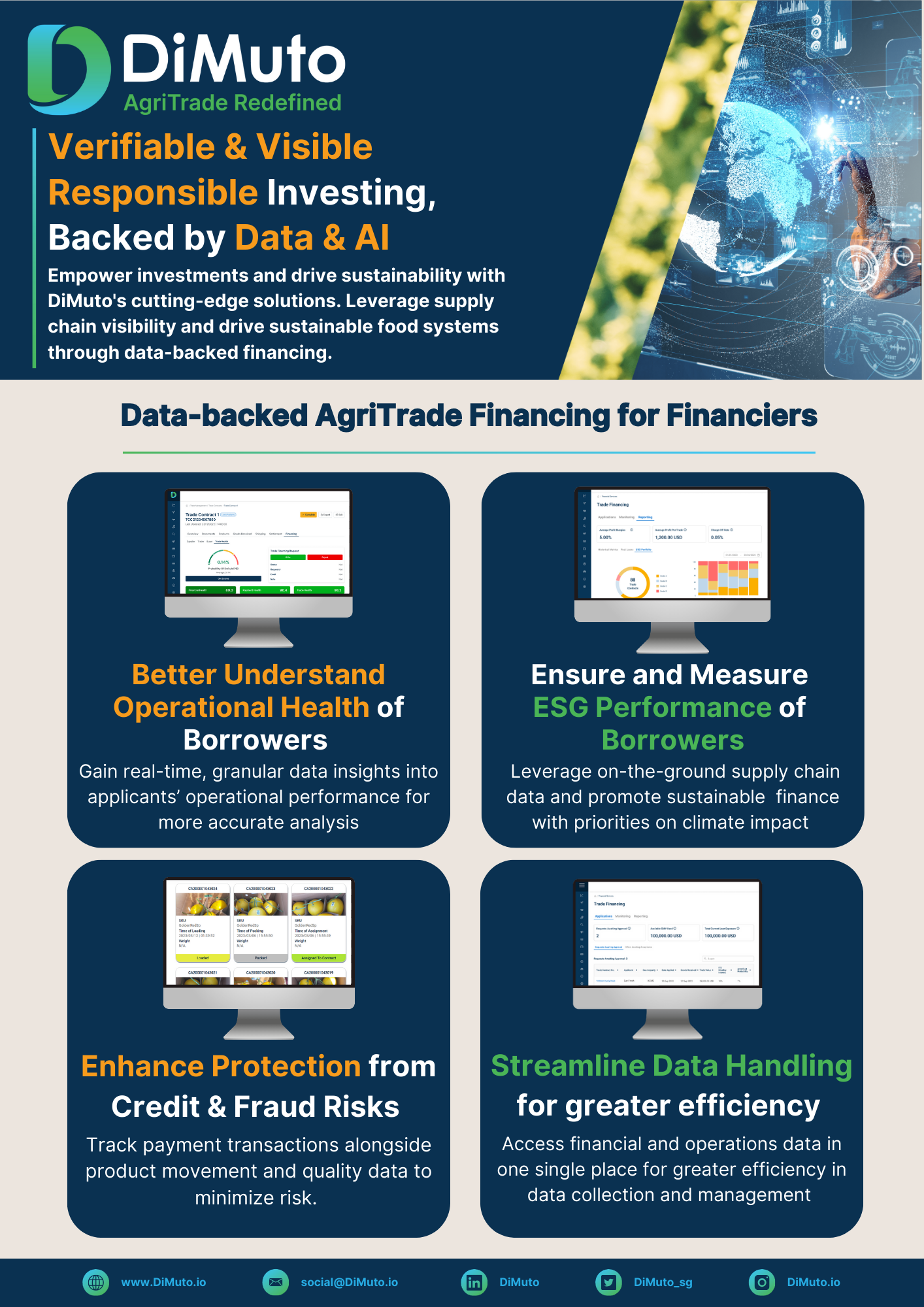
Download the DiMuto For Financier One Pager here.
DiMuto’s Environmental, Social, and Governance (ESG) Management feature is the latest addition to their all-in-one Trade Solutions Platform.
With automated drafting of Sustainability Report using AI Tools, DiMuto’s ESG Management Feature alleviates resource constraints that hinder ESG Reporting, simplifies regulatory compliance, and enhances AgriSMEs’ reputations as responsible businesses.
AgriFood businesses can now participate in DiMuto’s Digital Transformation to gain unprecedented visibility into their supplier programs, enabling them to enforce sustainability standards and build responsible supply chains.
Singapore, 20 September 2023 – Global AgriFood Digital Transformation Solutions company, DiMuto, announced the launch of its new Environmental, Social, and Governance (ESG) Management feature. This feature aims to empower AgriFood business owners with real-time insight into their ESG impact across their supply chains and determine opportunities for them to adopt sustainable solutions.
Today, AgriFood stakeholders are under increased scrutiny from consumers, investors, regulators, and civil society to ensure ethical practices, environmental conservation, and social responsibility. For example, the EU’s Corporate Sustainability Reporting Directive (CSRD) 2024 requires AgriFood companies to disclose their ESG practices throughout their value chains. As a result, companies are compelled to consistently report their ESG impact. However, obtaining consistent, complete, and reliable data is a major challenge in accurate sustainability reporting.
In particular, AgriSMEs face these challenges due to the lack of historical data within the industry and because they may not have the required knowledge, resources, or systems for complete data coverage. According to Ernst and Young, agriculture sectors often lack historical carbon emissions data as compared to other industries, such as oil and gas. Furthermore, research by the World Economic Forum finds that the complexity of ESG reporting discourages companies’ willingness and ability to report in accordance with established standards, especially for smaller or privately held companies. Thus, DiMuto’s ESG Management feature provides a comprehensive solution for AgriFood companies to track and monitor their sustainability performance.
Digital Transformation helps AgriFood businesses to better track and manage every step of their supply chain, with benefits including higher supply chain transparency, efficiency, and reduced operational costs. Together with DiMuto’s ESG Management feature, AgriFood companies can now immediately determine their food waste from rejected or discarded products, carbon emissions from shipments and electricity usage, and water usage across locational facilities. These 3 key data metrics are then aggregated automatically on DiMuto’s ESG Dashboard. This dashboard helps Agrifood business owners easily see the environmental impact of their operations and follow product lifecycles in real-time. Additionally, this data can be immediately generated into a report using AI Tools to be shared with relevant parties, helping AgriFood businesses save valuable time and resources. Consequently, companies can now easily navigate the complex ESG regulations landscape and ensure that they are able to comply with evolving standards. Furthermore, larger AgriFood companies can also take charge of their supplier programs, allowing them to assess their trade partners according to their sustainability standards or goals to build stronger and more responsible supply chains.
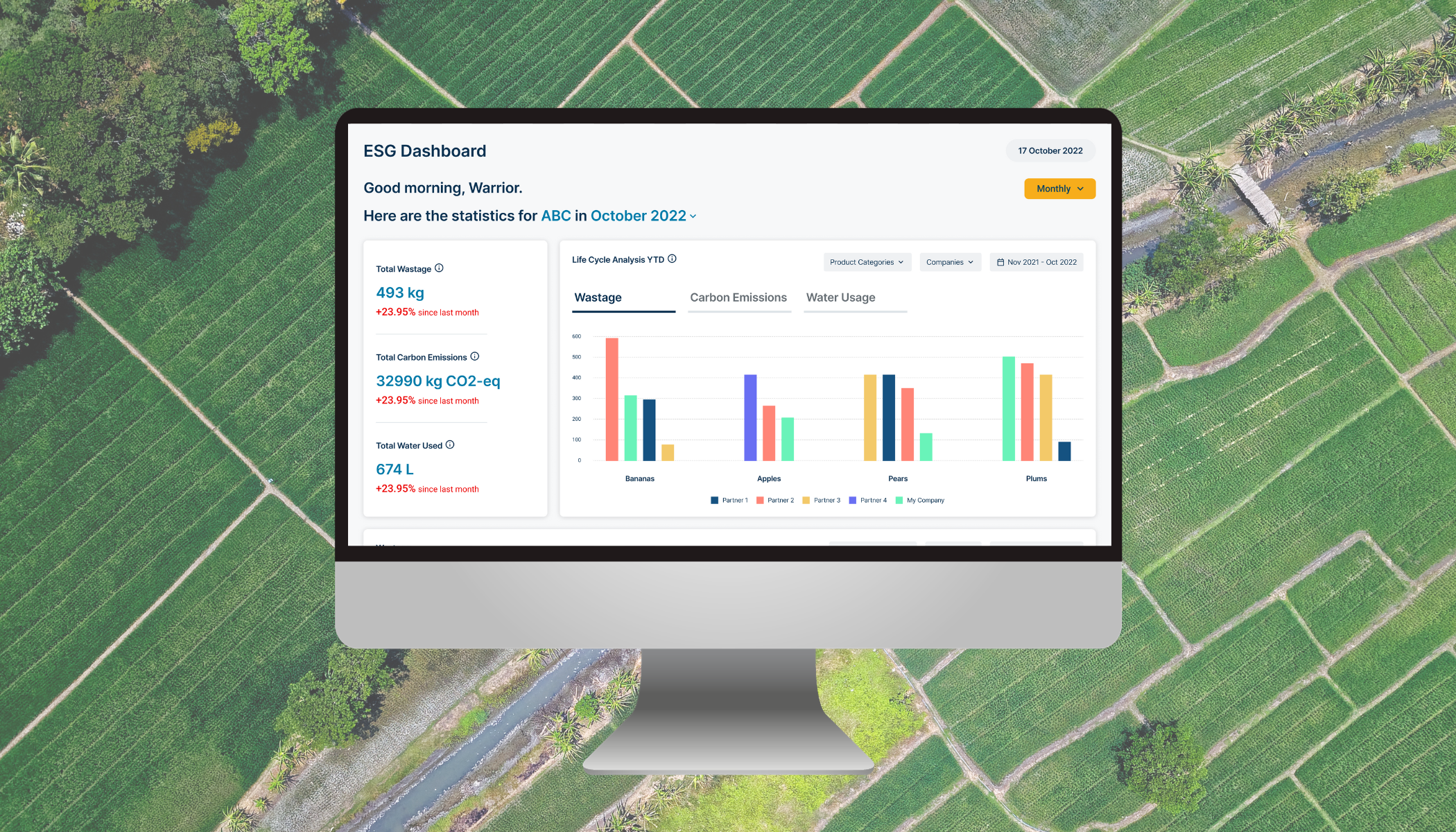
“DiMuto is excited to be at the forefront of redefining global AgriTrade through a digital transformation. We are providing innovative solutions to address the pressing sustainability challenges faced by companies today,” said DiMuto’s Founder CEO, Gary Loh. “Our ESG Management feature is a game-changer in helping companies to understand their carbon footprint and make data-driven decisions to increase their social impact and reduce their environmental impact. Furthermore, the feature is seamlessly connected with DiMuto’s other platform features, making it easy for our customers to use immediately.”
To ensure the integration and verification of this data, DiMuto’s ESG Management feature is built on blockchain technology and is connected to the existing Farm Management, Production Management, Trade Management, and Inspection Management features on the DiMuto Platform. DiMuto’s blockchain-powered solution helps to ensure immutability, showing the who, what, and when of data inputs for accurate tracking and monitoring of businesses’ environmental impact.
The ESG Management feature will provide companies with detailed analyses of their carbon footprint, including a breakdown of emissions by product, location, and transportation mode. This data will help companies make informed decisions about reducing their carbon footprint and ensure companies are aligned in meeting their environmental targets.
“DiMuto’s ESG Management feature is a key step towards a more sustainable future,” said HuiMin Lee, DiMuto’s Chief Experience Officer. “We believe that companies have a responsibility to take action on sustainability, and we are committed to providing the tools and solutions to make this a reality.”
DiMuto is committed to driving positive change in the AgriFood industry and helping companies achieve their sustainability goals. The feature is now available to all companies using the DiMuto platform.
-end-
About DiMuto
DiMuto redefines AgriTrade with AI, Data Visibility, and Finance — Using tech to create and connect a sustainable, global AgriTrade ecosystem.
With our three pillars of Marketplace, Trade Management, and Trade Financing, DiMuto supports every aspect of AgriFood trading, redefining the way goods are managed from farm to table, seamlessly and simply connecting every step, and making it visible throughout.
By traders for traders, we help AgriFood business owners optimize their operations efficiently and for them to build a foundation of trust between their buyers or sellers so that they can take action on improving and growing their businesses in a more sustainable, efficient manner.
Maximizing Business Efficiency, Minimizing Impact on The Planet.
Since 2019, DiMuto has successfully tracked and traced over millions of pieces in produce and millions in dollars of trade value on our platform, working with a global portfolio of clients in over ten countries and five continents. DiMuto is founded by Chief Executive Officer Mr Gary Loh, who is also the Executive Chairman of First Alverstone Group.
For more information, please visit www.dimuto.io.
Updated: 26 April 2021
DiMuto Digital Transformation Solutions: Elevate Your Business with Digital Transformation
In today’s fast-paced world, the Agrifood industry faces numerous challenges, from supply chain inefficiencies to consumer demands for transparency. That’s where DiMuto comes in, offering a cutting-edge solution to digitize, digitalize, and transform your operations. Elevate your AgriTrade business with DiMuto’s game-changing Digital Transformation Solutions. Join DiMuto now to cultivate a future of success and impact in the world of agriculture trading.
Download the DiMuto Digital Transformations One Pager here.
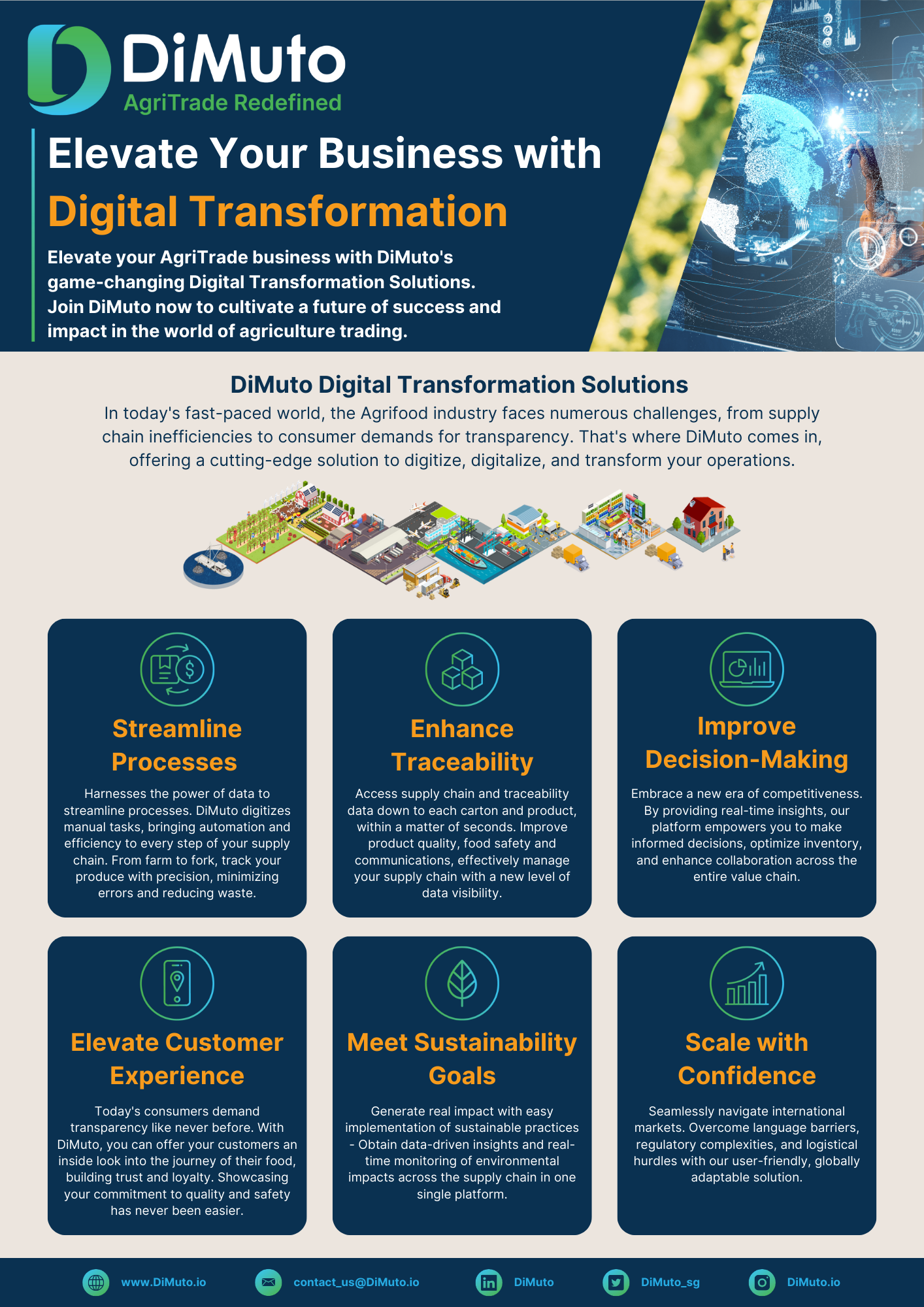
[Whitepaper]
There is increasing pressure from consumers, investors, regulators, and civil society to ensure AgriFood stakeholders align with ethical practices, environmental conservation, and social responsibility. This is why DiMuto is committed to providing an accessible digital solution to empower AgriFood businesses to plan, measure, and communicate such critical ESG information.
We are excited to release our latest whitepaper, titled “Digital Transformation: A Pathway to Sustainable AgriTrade”, which aims to guide AgriFood stakeholders in understanding the symbiotic relationship between ESG visibility and Digital Transformation to foster a more sustainable and technologically advanced supply chain ecosystem.
Explore the opportunities Digital Transformation offers the AgriFood industry to enhance ESG visibility. Together, we can build a resilient, socially and environmentally responsible global food system.
Download the DiMuto Whitepaper here.